What is AM
Using computer aided design (CAD) or 3D object scanners, additive manufacturing (AM) allows for the creation of objects with precise geometric shapes. These are built layer by layer, as with a 3D printing process, which is in contrast to traditional manufacturing that often requires machining or other techniques to remove surplus material.
Similar to standard 3D printing, AM allows for the creation of bespoke parts with complex geometries and little wastage. Ideal for rapid prototyping, the digital process means that design alterations can be done quickly and efficiently during the manufacturing process. Unlike with more traditional subtractive manufacturing techniques, the lack of material wastage provides cost reduction for high value parts, while AM has also been shown to reduce lead times. In addition, parts that previously required assembly from multiple pieces can be fabricated as a single object which can provide improved strength and durability. AM can also be used to fabricate unique objects or replacement pieces where the original parts are no longer produced.
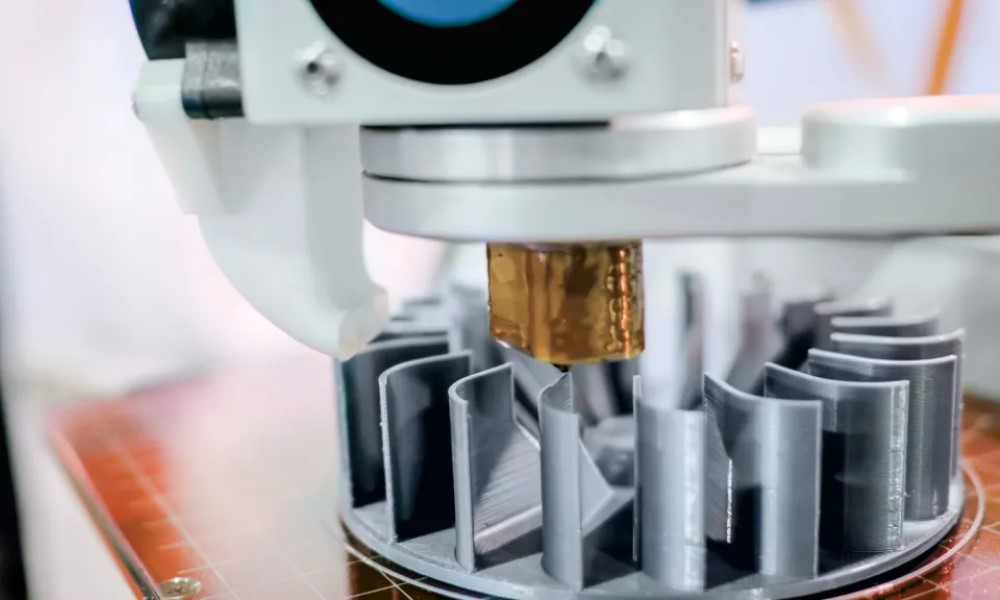
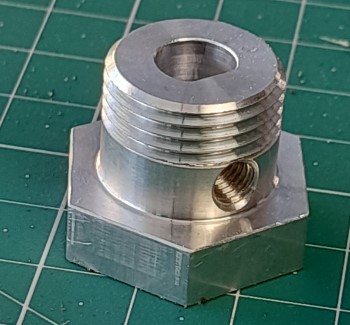
Material: Aluminium 6061
Single Unit Cost: $88.70
Single Unit Weight: 14.5 grams
Time to deliver: 5 days
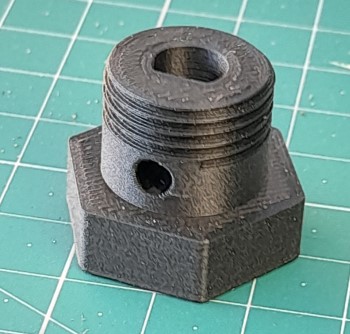
Material: CF-HTPLA
Single Unit Cost: $4.75
Single Unit Weight: 6 grams
Time to deliver: within 24hrs
Advantages
-
Accelerated time to market
Reduced timeline from design to completed component
Our AM services provide you with the ability to rapidly produce viable components, whether they're for POC or finished product.
-
Reduced costs
The AM process is based on adding only the amount of material required to achieve the finished shape making the process inherantly cheaper, this plus other factions goes towards our ability to produce your component chaeper than the normal Subtractive process.
-
Supply chain consolidation
Due to the local nature of our AM facility supply chain issues are reduced. Digital files can be archived in our servers for call up any time. Our facility operates 24/7/52 - basically it never closes. This enables you to reduce your inventory holding costs as we can schedule the production of your components within hours of receiving the order.
-
Multiple iterations
Multiple iterations are easier to manage and tend to compound the overall project savings in terms of actual cost and environment impact. Generally multiple 3D print iterations can be achieved in the same time usually required for a single unit via a subtractive process.
-
Part consolidation
The traditional Subtractive process has many limitations as to the complexity of the components it can create resulting in the need to machine multiple parts that are combined to develop a single useful component. This can be quite wasteful in terms of time, energy costs, material costs, labour costs (maching and assembly) and finally the overall weight of the assembled component. As the Additive process resides in the digital domain quite complex and organic components can be designed and produced. Components can be designed more effectively around stress points resulting in stronger components with less material.
-
Low and mid volume production
Generally because of our facility we can produce multiple components at the same time meaning a shorter delivery timeframe.
-
Reduced waste
The most obvious difference between Additive and Subtractive manufacturing is the lack of waste as a result of the Additive process. In the Subtractive process you generally start out with a solid block or bar of the material to be used; through varies operations material is removed until the final shape is achieved. It's not unusual for at least 40% of the base material to be machined away as waste. The Additive process is the complete opposite; parts are built up as a finished design. Waste is minimised as a part of the preparation (Slicing) process. This advantage is compounded where multiple parts can be combined into a single 3D printed component.
Gallery
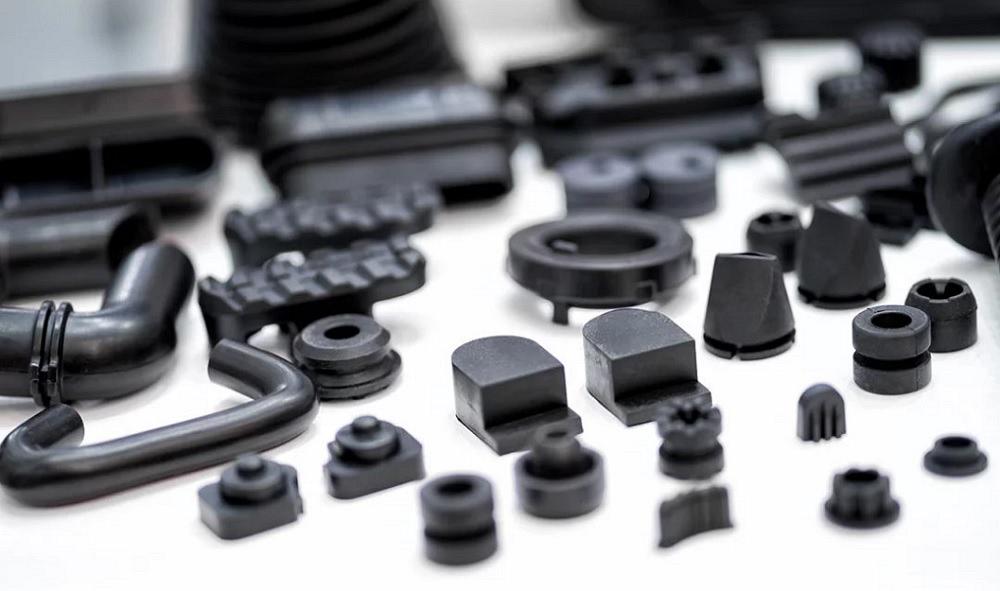
Our Services
Carbontek provides an industrial grade additive manufacturing service to various industries and sectors. Our print farm enables small volume manufacturing of components as well as one-off prototypes for proof of concept development.
Our services include a full design and reverse engineering capability.
If you are wanting to set up your own in-house facility we can provide the expertise, equipement and on-going support to get you up and running.
3D Print Farm
- FDM
- Resin
- Laser sintered metal
Reverse Engineering
- 3D Laser scanning
- 3D CAD developmen
- 3D CAD design
Prototyping
- 3D CAD design
- FEA Analysis
- CNC routing and fabrication
Sales and Consulting
- Flashforge distributor
- Print farm setup and installation
- Print farm management solutions
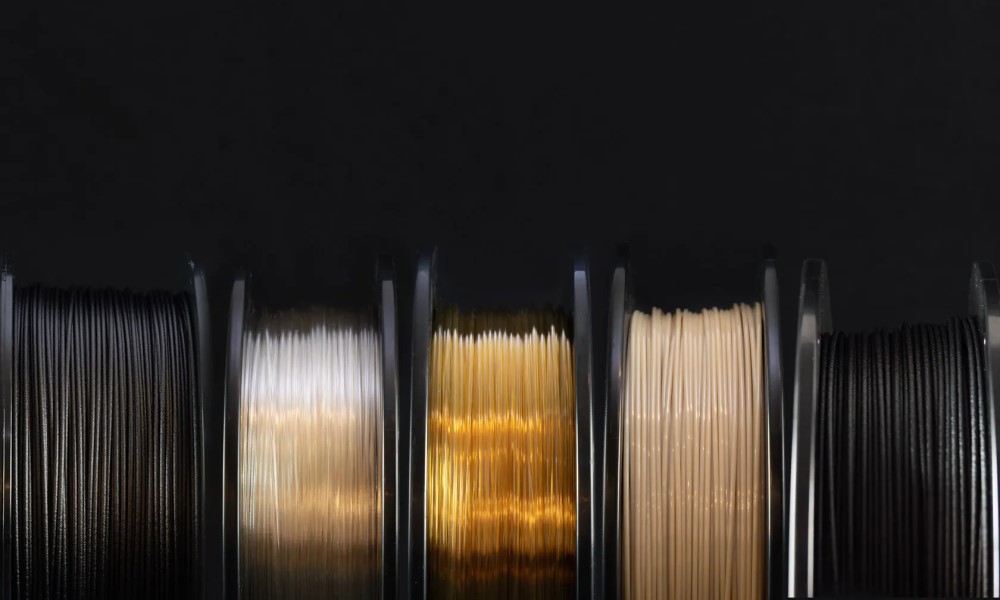
Materials
Flex - TPU85A / TPE / TPB / TPC
PC / PA / PP / PETG / ASA / ABS / PLA / CF-HTPLA / PC-ABS / PAHT
PACF / PET-CF / PP-CF / PA-GF / PC-ABS / PP-GF / PPS-CF / PPS
Metals - Aluminium / Inconel / Titanium
Whatever your requirement we have you covered. If you're unsure of the best option, get in touch with us and we'll recommend a solution based on your needs.
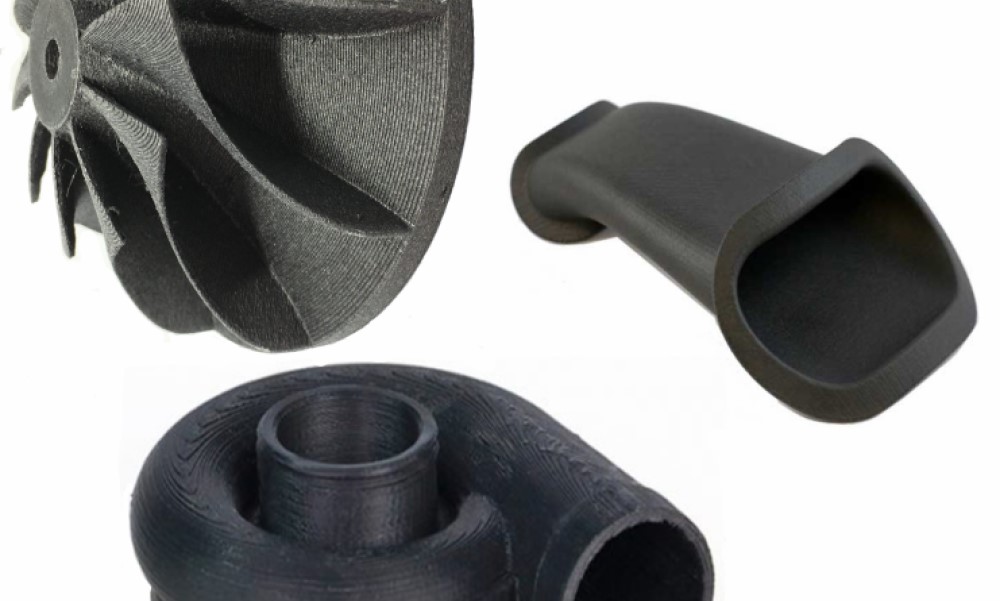
Applications
Due to the versatility of the process, 3D printing has applications across a range of industries, for example:
3D printing is used across the aerospace (and astrospace) industry due to the ability to create light, yet geometrically complex parts, such as blisks. Rather than building a part from several components, 3D printing allows for an item to be created as one whole component, reducing lead times and material wastage.
The automotive industry has embraced 3D printing due to the inherent weight and cost reductions. It also allows for rapid prototyping of new or bespoke parts for test or small-scale manufacture. So, for example, if a particular part is no longer available, it can be produced as part of a small, bespoke run, including the manufacture of spare parts. Alternatively, items or fixtures can be printed overnight and are ready for testing ahead of a larger manufacturing run.
The medical sector has found uses for 3D printing in the creation of made-to-measure implants and devices. For example, hearing aids can be created quickly from a digital file that is matched to a scan of the patient's body. 3D printing can also dramatically reduce costs and production times.
The rail industry has found a number of applications for 3D printing, including the creation of customised parts, such as arm rests for drivers and housing covers for train couplings. Bespoke parts are just one application for the rail industry, which has also used the process to repair worn rails.
The speed of manufacture, design freedom, and ease of design customisation make 3D printing perfectly suited to the robotics industry. This includes work to create bespoke exoskeletons and agile robots with improved agility and efficiency.